Soft robots are revolutionizing the world of robotics, allowing machines to operate in ways that traditional robots never could. These robots, made from flexible materials, can bend, twist, and deform, making them ideal for working in challenging environments.
However, this flexibility also makes them more prone to damage, which has limited their widespread application - until now. Engineers at the University of Sheffield have developed a groundbreaking valve that makes soft robots significantly more resilient. Thus, allowing them to recover from damage and keep performing their tasks.
This remarkable innovation, reported in Science Robotics, was spearheaded by Dr. Marco Pontin and Dr. Dana Damian from the University’s School of Electrical and Electronic Engineering. Their new valve design can automatically adjust a robot’s internal pressure and isolate any damaged parts.
How Soft Robots Work?
Soft robots are fascinating pieces of technology. Unlike traditional robots, which are built from rigid parts like metals and plastics, soft robots are made from highly flexible materials such as silicone, rubber, and various polymers. This flexibility allows them to squeeze into tight spaces, adapt to unpredictable environments, and perform delicate operations.
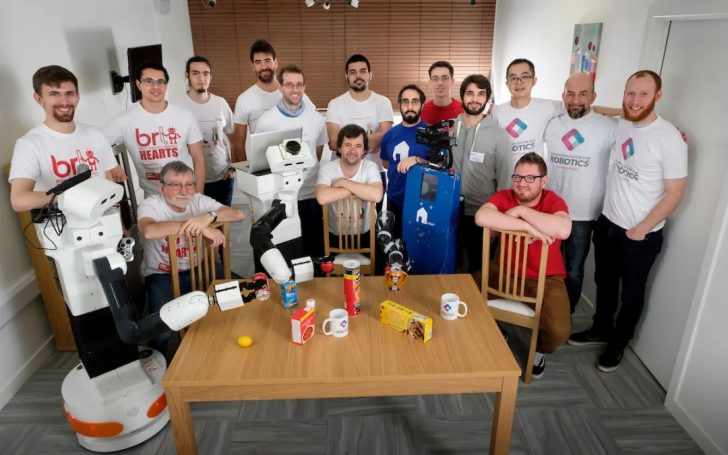
Tech Center / Unlike traditional robots, soft robots are made from highly flexible materials such as silicone, rubber, and various polymers.
However, the same materials that make these robots so adaptable also make them vulnerable. Their soft, pliable structure is susceptible to tears, punctures, or other types of damage. Even a small rupture could cause the robot to fail, rendering it useless until repairs can be made.
Vulnerability to Damage Has Been a Major Concern
One of the main challenges facing soft robots is their susceptibility to damage. Because they are designed to bend, stretch, and twist, soft robots are often exposed to forces that can easily tear their flexible materials. A small puncture or a burst can quickly lead to a larger failure, making the entire robot ineffective.
In many cases, this vulnerability limits where soft robots can be used. For example, a soft robot working inside the human body could be dangerous if it failed during a medical procedure. Similarly, a robot operating underwater could be damaged by pressure or sharp objects.
In space, where conditions are harsh and unforgiving, a single tear could compromise an entire mission. The flexibility of soft robots, while incredibly useful, has been their Achilles' heel.
The Resilient New Valve Offers a Much-Awaited Solution
The breakthrough at the University of Sheffield offers a promising solution to this problem. Dr. Marco Pontin and Dr. Dana Damian have developed a new type of valve that helps soft robots better manage the risk of damage. Their valve automatically adjusts the internal pressure within the robot and isolates any section that has been damaged. Essentially, the valve prevents the damaged area from affecting the rest of the robot, allowing the robot to keep functioning even when one part is compromised.
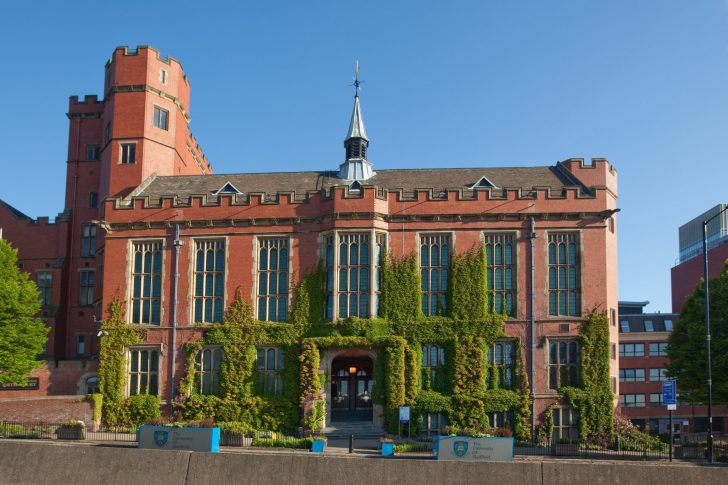
Marca / The ability to contain damage and keep operating makes soft robots much more reliable in high-stakes environments.
Be it performing life-saving surgery or exploring deep ocean trenches, these robots can now keep working even if part of their structure is damaged. This resilience could open the door to many new applications for soft robots, pushing the boundaries of what they can achieve.
However, the valve designed by the University of Sheffield engineers operates in a clever way. When a section of the robot experiences a rupture or puncture, the valve senses the change in pressure and immediately reacts by closing off the damaged section.
Notice, this prevents the damage from spreading throughout the robot. Something that would typically cause a total failure. The valve then maintains pressure in the undamaged parts of the robot, allowing it to continue its task while repairs are made later.